We use the same formula for calculating the working life expectation of ball bearings of all qualities.
Ball bearings with a higher level of precision have a much longer working life than those with wider tolerances, although the latter support more play.
The tables describing the dimensions and the characteristics of the ball bearings also include a factor Y, determined by the allowed static load.
These first measurements allow you to obtain the fl factor according to the formula:
fl = X • Y • P
fl = coefficient of the working life expectation
X = coefficient of shaft hardness
Y = dynamic coefficient of the ball bearing
P = load perpendicular to the ball bearing [Kp]
The Diagram 1 gives us the working life expectation in metres.
The working temperature influences the working life expectation and must be taken into consideration in the calculation by the Z factor according to Table 2.
The given formula is valid for a maximum deflection of 0,001 mm along the total length of the supporting balls. It is imperative not to use untempered hard-chrome shafts. In case of doubt, do not hesitate to consult us before starting a new combination. We are at your disposal for all information, and will not hesitate to advise against the use of a SFERAX ball bearings when the
application is unsuitable.
Example
These calculations are only theoretical and therefore do not necessarily correspond to the actual conditions. SFERAX SA cannot be held responsible for them.
The vertical charge of the machine slide is 100 kp*), moving on 2 shafts and supported by 4 type OUV ball bearings. Each ball bearing carries 25 kp*). The stroke slide is 400 mm, moving 200 times per minute.
Shaft hardness: 60 HRC.
Working temperature: 120° C.
Preferred shaft diameter: 30 mm
P = 25 Kp*)
Y = 0,000152 (see product sheet)
X = 1,1 (Table 1)
Distance run per hour = 0,4 • 2 • 60 • 200 = 9’600 m/h.
fl = X • Y • P = 1,1 • 0,000152 • 25 = 0,00418
Working life at 120° C = plus de 800’000’000 (diagram 1)
Working life at 120° C. = 0,92 • 800 • 106 = 736 • 106 m (Z = 0,92)
Working life in hours = (736 / 9'600) • 106 = 76’666 hours.
*1 Kp = 9.81 N
Table 1
Coefficient of the Shaft Hardness
|
Rockwell C
|
X
|
Rockwell C
|
X
|
Rockwell C
|
X
|
51
|
1,93
|
56
|
1,27
|
61
|
1,085
|
52
|
1,74
|
57
|
1,19
|
62
|
1,07
|
53
|
1,58
|
58
|
1,15
|
63
|
1,06
|
54
|
1,45
|
59
|
1,12
|
64
|
1,05
|
55
|
1,35
|
60
|
1,10
|
65
|
1,04
|
Table 2
Temperature Coefficient
|
Temp.
° Celsius
|
Z
|
80°
|
1,00
|
125°
|
0,92
|
140°
|
0,88
|
150°
|
0,85
|
180°
|
0,77
|
Diagramme 1
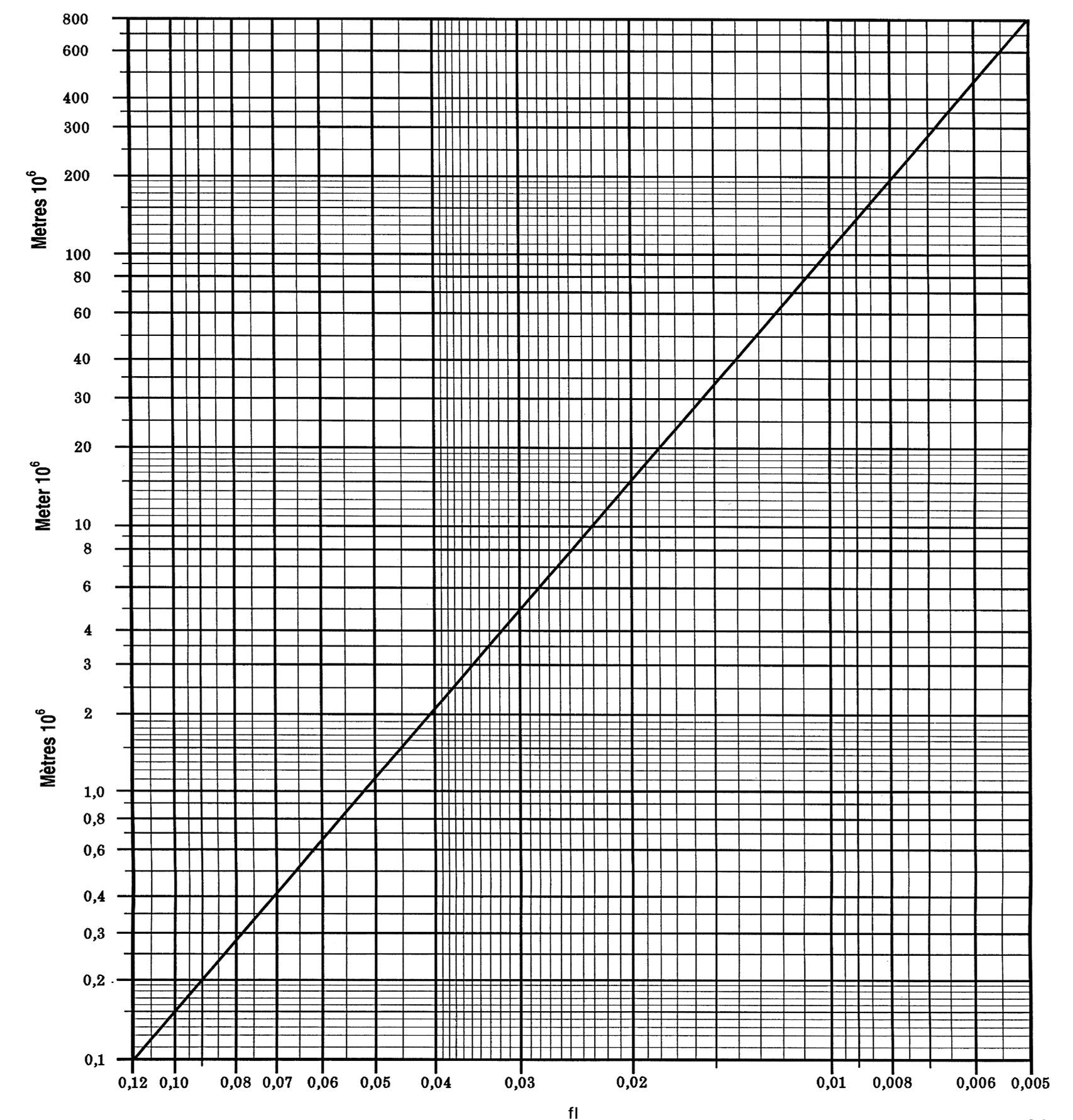